

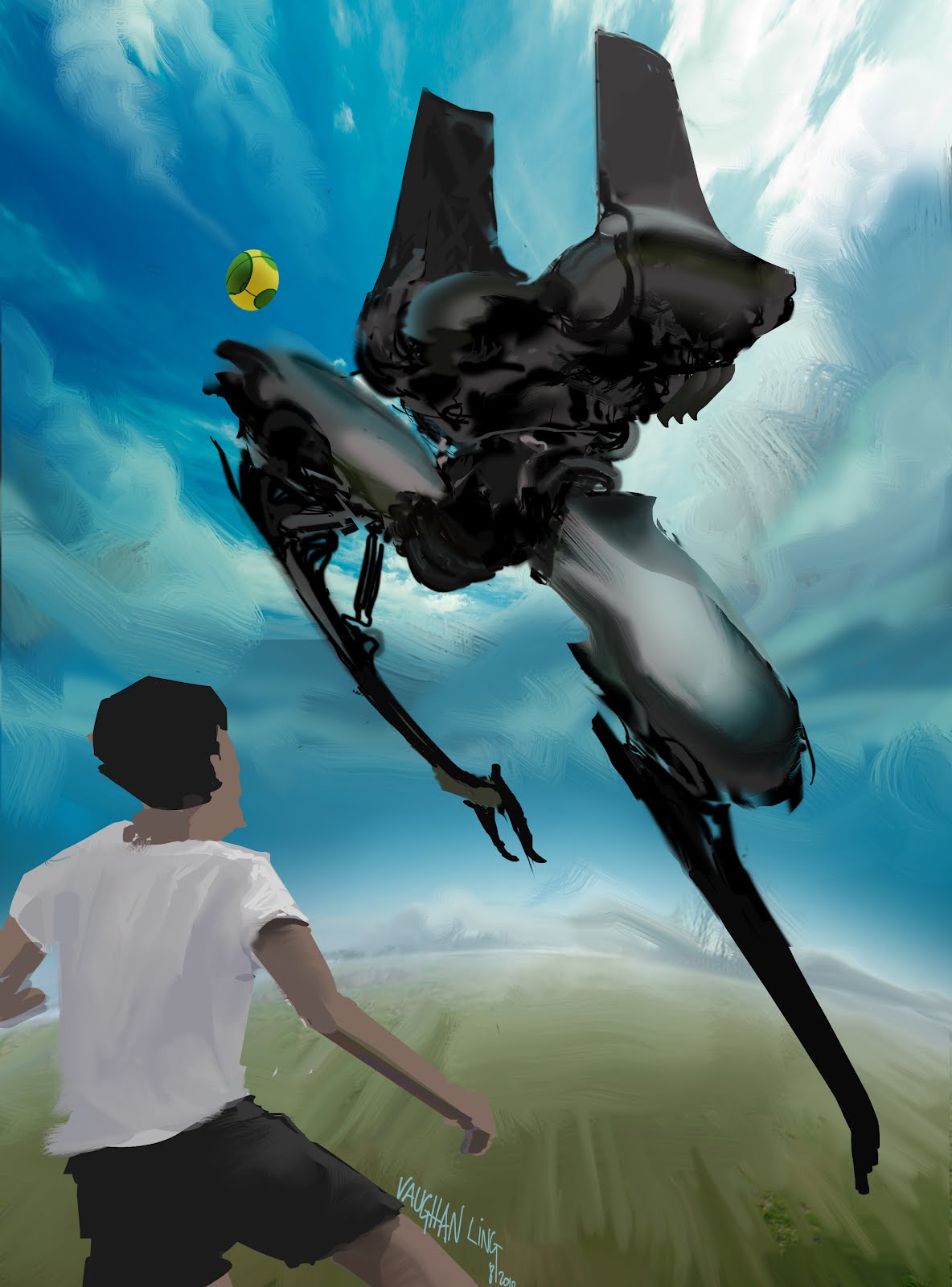
The basic block diagram of the closed-loop control system is shown in Figure 1. For obtaining satisfactory responses and characteristics for the closed-loop control system, an additional system, called as compensator or controller, can be added to the loop. The difference between the actual response (calculated) of the płant and the desired response gives the error signal. The output of the physical system under control is adjusted by the help of an error signal. The basic control problem is given as follows: In a closed-loop control system, forcing signals of the system inputs are determined by the output responses of the system. A sensor measures the controlled signal, A plant is a physical system under control. The first step toward controlling any physical variable is to measure it. Closed-Hoop control systems are also known as feedback control systems. On the other hand, in a closed-loop control system, the input control action depends on the physical system output. In open-loop control systems, the input control action is independent of the physical system output. There exist two types of control systems: open-loop and closed-loop control systems. Compared to conventional control techniques, FLC has been best utilized in complex ill-defined problems, which can be controlled by an efficient human operator without knowledge of their underlying dynamics.Ī control system is an arrangement of physical components designed to alter another physical system so that this system exhibits certain desired characteristics. The application of FLC extends from industrial process control to biomedical instrumentation and securities.
#FUZZY ROBOT IMAGEGIF CODE#
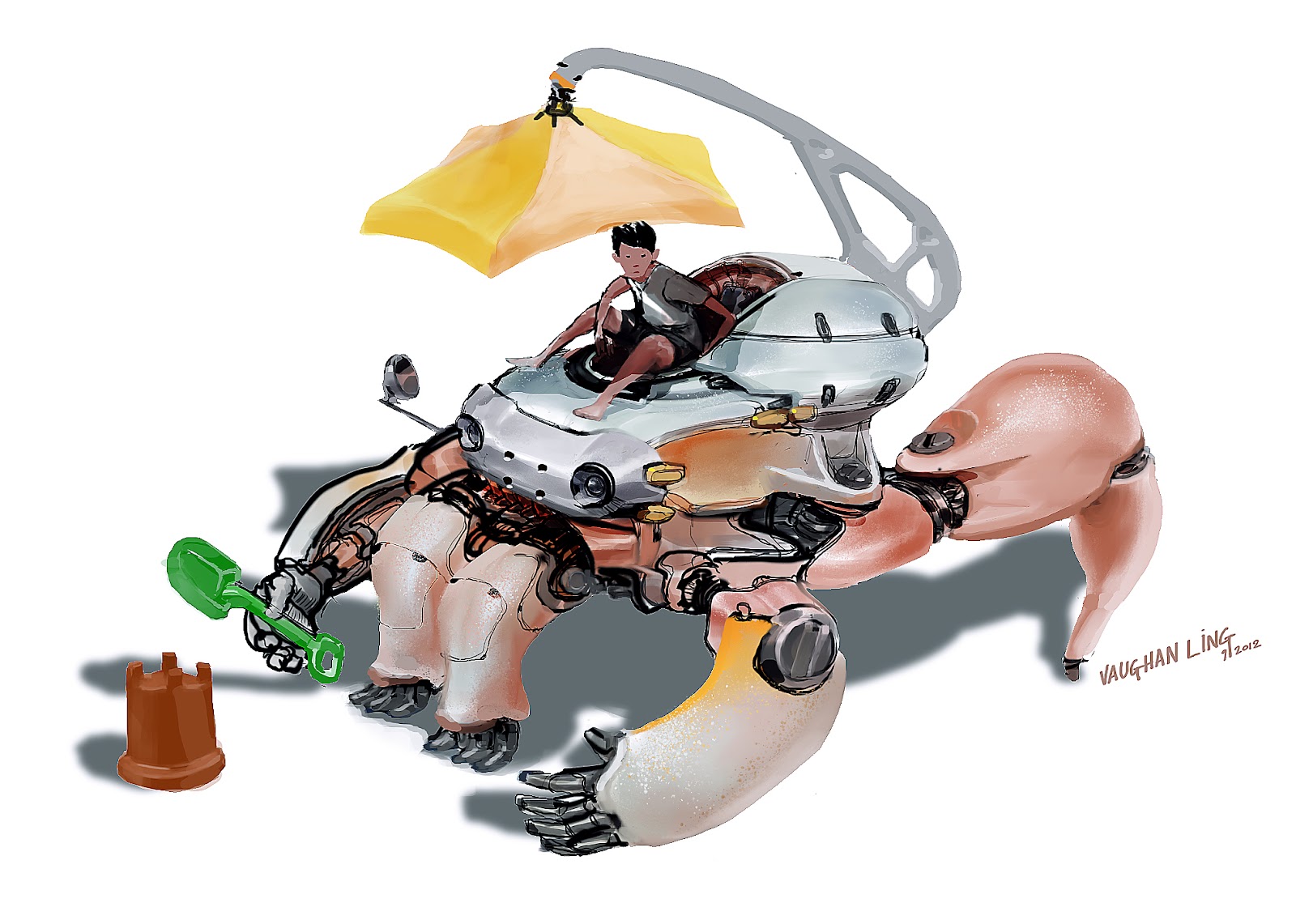
As a new method, an error between desired force and measured force and momentum or robot manipulator are used as input signals of the controller.
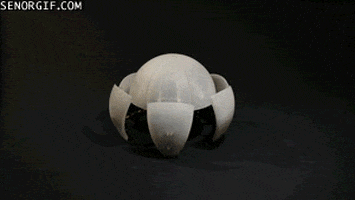
A robot manipulator controller for force control is designed using fuzzy logic in order to realize human like control and then modeled as a neural network to adjust membership functions and rules to achieve desired force control. In this paper, fuzzy-neural controller is introduced for robot manipulator force control to an unknown environment. Simulation has done to confirm the effectiveness of the controller.ĪB - In these days, fuzzy-neural control, the combination of neural networks control which has a learning ability from experiments and fuzzy control which has an ability of dealing with human knowledge, has been studied in order to make up for each other's weak points. N2 - In these days, fuzzy-neural control, the combination of neural networks control which has a learning ability from experiments and fuzzy control which has an ability of dealing with human knowledge, has been studied in order to make up for each other's weak points. T1 - Fuzzy neural controller for robot manipulator force control
